What is Porosity in Welding: Best Practices for Avoiding Porous Welds
What is Porosity in Welding: Best Practices for Avoiding Porous Welds
Blog Article
The Scientific Research Behind Porosity: A Comprehensive Guide for Welders and Fabricators
Recognizing the elaborate mechanisms behind porosity in welding is crucial for welders and fabricators making every effort for remarkable craftsmanship. As metalworkers dive right into the depths of this phenomenon, they discover a world controlled by different variables that influence the development of these small gaps within welds. From the structure of the base materials to the details of the welding procedure itself, a multitude of variables conspire to either aggravate or ease the existence of porosity. In this comprehensive overview, we will unwind the science behind porosity, exploring its results on weld quality and introduction progressed strategies for its control. Join us on this trip with the microcosm of welding blemishes, where precision satisfies understanding in the search of flawless welds.
Comprehending Porosity in Welding
FIRST SENTENCE:
Evaluation of porosity in welding exposes critical understandings into the integrity and top quality of the weld joint. Porosity, identified by the visibility of tooth cavities or spaces within the weld steel, is a typical issue in welding processes. These gaps, otherwise effectively dealt with, can jeopardize the structural integrity and mechanical residential or commercial properties of the weld, resulting in potential failures in the ended up item.
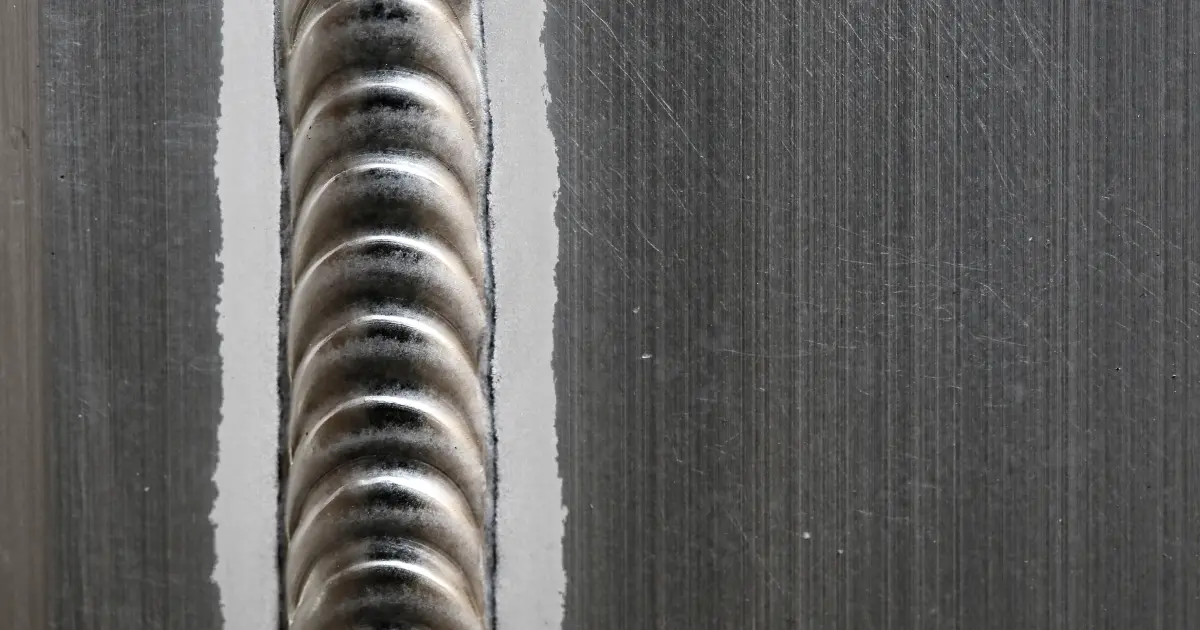
To spot and quantify porosity, non-destructive testing techniques such as ultrasonic testing or X-ray inspection are usually used. These methods permit the recognition of inner defects without jeopardizing the stability of the weld. By assessing the dimension, form, and circulation of porosity within a weld, welders can make enlightened choices to enhance their welding procedures and accomplish sounder weld joints.
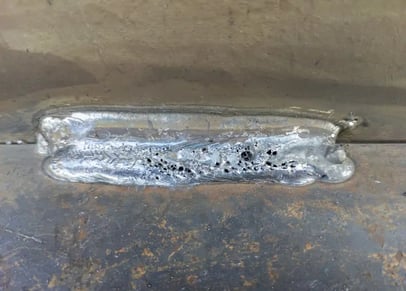
Factors Influencing Porosity Development
The incident of porosity in welding is affected by a myriad of factors, ranging from gas securing effectiveness to the details of welding parameter setups. Welding criteria, including voltage, current, travel rate, and electrode type, also effect porosity development. The welding strategy utilized, such as gas metal arc welding (GMAW) or secured steel arc welding (SMAW), can influence porosity formation due to variations in warmth circulation and gas insurance coverage - What is Porosity.
Results of Porosity on Weld Top Quality
Porosity development significantly compromises the structural integrity and mechanical homes of bonded joints. When porosity is present in a weld, it produces voids or tooth cavities within the product, decreasing the overall toughness of the joint. These gaps act as anxiety focus points, making the weld much more prone to cracking and Continued failing under load. The presence of porosity additionally compromises the weld's resistance to deterioration, as the entraped air or gases within the gaps can react with the surrounding environment, bring about degradation gradually. Furthermore, porosity can prevent the weld's ability to withstand stress or influence, further endangering the overall high quality and dependability of the bonded framework. In vital applications such as aerospace, vehicle, or architectural buildings, where safety and sturdiness are paramount, the harmful results of porosity on weld top quality can have extreme effects, highlighting the significance of reducing porosity via correct welding strategies and treatments.
Methods to Minimize Porosity
In addition, making use of the ideal welding criteria, such as the proper voltage, current, and linked here travel speed, is critical in preventing porosity. Preserving a regular arc length and angle throughout welding additionally helps lower the possibility of porosity.

Moreover, choosing the right shielding gas and keeping proper gas circulation prices are vital in decreasing porosity. Using the ideal welding technique, such as back-stepping or utilizing a weaving activity, can also aid distribute warmth equally and lower the opportunities of porosity development. Making sure correct ventilation in the welding atmosphere to eliminate any kind of prospective resources of contamination is essential for accomplishing porosity-free welds. By carrying out these methods, welders can properly minimize porosity and create top notch bonded joints.
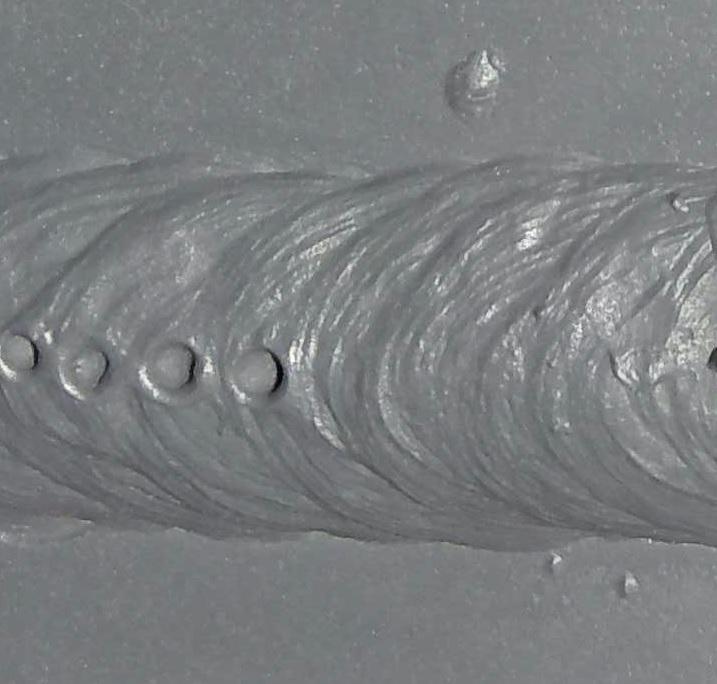
Advanced Solutions for Porosity Control
Executing cutting-edge technologies and innovative approaches plays an essential function in achieving exceptional control over porosity in welding procedures. Furthermore, using sophisticated welding methods such as pulsed MIG welding or changed atmosphere welding can additionally aid alleviate porosity problems.
One more innovative solution entails using advanced welding equipment. As an example, using tools with built-in functions like wikipedia reference waveform control and innovative power resources can improve weld quality and minimize porosity threats. The application of automated welding systems with precise control over parameters can considerably reduce porosity flaws.
Moreover, integrating sophisticated tracking and examination technologies such as real-time X-ray imaging or automated ultrasonic testing can aid in identifying porosity early in the welding process, permitting for prompt corrective activities. On the whole, incorporating these sophisticated options can greatly improve porosity control and enhance the general high quality of bonded components.
Verdict
To conclude, comprehending the science behind porosity in welding is essential for welders and fabricators to generate high-grade welds. By identifying the variables influencing porosity development and carrying out methods to minimize it, welders can boost the total weld top quality. Advanced solutions for porosity control can better enhance the welding procedure and make sure a strong and reputable weld. It is necessary for welders to constantly educate themselves on porosity and execute best practices to attain optimum results.
Report this page